FAQ
Looking for more information about a Reliable product?
Our Product Technology team has compiled a list of frequently asked questions to help you get the information you need. Jump to a product category using the links below.
Can’t find what you’re looking for?
Contact Product Technology at technicalservices@reliablesprinkler.com or call 1.800.557.2726
Sprinklers
The liquid used in our glass bulb sprinklers is a non-toxic proprietary glycerin solution that expands when heated.
The different colors designate various temperature classification ratings in accordance with NFPA 13.
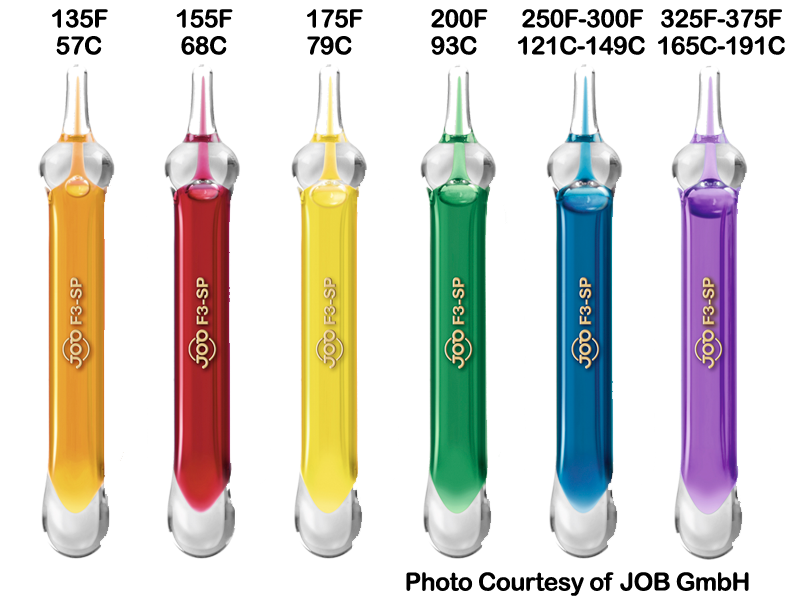
The different size bulbs relate to the Response Time Index (RTI) of the sprinkler. This measure determines the type of sprinkler response. 5mm bulbs are used for standard response sprinklers, 3mm bulbs are used for quick response sprinklers, and 2.5mm bulbs are used for ESFR’s and Fixed Temperature Release Pilot Line Detectors (PLD).
The RASCO marking is indicative of a Reliable manufactured product. Additional information, including the Sprinkler Identification Number (SIN), can be found on the sprinkler.
Reliable offers several corrosion resistant coatings and sprinklers manufactured from stainless steel. Most sprinklers are available with a polyester coating in various colors. In addition, for standard response sprinklers we offer 165°F clear wax, 212°F brown wax (for intermediate temperature rated sprinklers), lead plated, and wax over lead coatings. Most glass bulb sprinklers are also available with an electroless nickel PTFE (ENT) finish. Reliable ENT finish sprinklers are cULus Listed and, in some cases, FM Approved as Corrosion Resistant Sprinklers. The technical bulletin for each sprinkler will provide details on corrosion resistant finishes and applicable listings.
Standard spray sprinklers, such as the Model F1 series, Model F1FR series, and Model G series are control mode/density area sprinklers available with different orifice sizes and K-Factors. The amount of water discharged is dependent on the spacing and density requirements in accordance with NFPA 13. The pressure to achieve that flow is based on the K-Factor of the sprinkler and the pressure available based the available water supply. You must calculate the pressure required using the formula P = (Q/K)². Alternately, if the pressure at the sprinkler is known, calculate the flow using the formula Q = K√(P). NFPA 13 requires a minimum starting pressure of 7 psi for most sprinklers.
Q = Flow (in gpm)
K = K-Factor
P = Pressure (in psi)
This depends on the sprinkler. Generally speaking, NFPA 13 has no height restrictions on the use of control-mode density-area (CMDA) sprinklers except in certain storage occupancies. Control mode specific application (CMSA) and early-suppression fast-response (ESFR) sprinklers used in the protection of storage are generally limited by specific roof or ceiling heights. Chapters 12 through 21 of NFPA 13 address the protection of storage using CMDA, CMSA, and ESFR sprinklers.
NFPA specifies the minimum spacing for sprinklers, but also states that sprinklers must be installed in accordance with their listing in the event that the listed minimum distance differs from the standard. Reliable indicates the minimum spacing on all sprinklers that differ from NFPA 13, NFPA 13R and NFPA 13D standards. If not shown in the bulletin, the minimum spacing is as allowed by the applicable NFPA standard.
Recessed and concealed sprinkler ceiling plates are required to be listed with the sprinkler, and used only in accordance with their listing. Mixing and matching of recessed trim and concealed ceiling plates is prohibited. Exposed or surface mount sprinklers can use any trim plate provided that the deflector distances specified in NFPA 13 are met.
The Reliable SWC concealed horizontal sidewall can be used in Light Hazard areas as defined in NFPA 13 and non-residential Light Hazard areas as defined in NFPA 13R. It is not a residential sprinkler, and therefore cannot be used in applications requiring a listed residential sprinkler. You should always check for state or local requirements that might differ from the NFPA codes.
Reliable never produced a large drop sprinkler. In the 2010 edition of NFPA 13, Large Drop sprinklers were redesignated as Control Mode Specific Application Sprinklers (CMSA). Most advantages of Large Drop sprinklers have been superseded by ESFR technology.
While it does not fit strictly within the confines of the CMSA requirements of NFPA 13, Reliable offers the Model N252 EC CMSA sprinkler (technical bulletin 908) that can be used in conjunction with the “Alternative Sprinkler System Designs” section of NFPA 13. The Model N252 EC CMSA enjoys significant water saving advantages compared to standard sprinklers and with the adoption of the 2015 International Fire Code, smoke and heat removal systems are no longer required. This makes the Model N252 EC CMSA an attractive option to other conventional protection schemes.
Yes, Reliable manufactures several styles of stainless steel sprinklers. Please reference Technical Bulletin 064 for standard response stainless steel sprinklers, Technical Bulletin 065 for quick response stainless steel sprinklers, and Technical Bulletin 178 for Extended Coverage stainless steel sprinklers.
Dry sprinklers should always be installed in the side outlet of a tee. The fitting on the dry sprinkler is designed to extend up into the fitting to prevent the accumulation of deposits on the inlet of the sprinkler. Dry sprinklers should never be installed in an elbow or coupling; this can impede operation and/or allow deposits to accumulate on the inlet of the dry sprinkler. NFPA 13 and our installation instructions specify the minimum exposed barrel length required inside the conditioned space depending on the anticipated temperatures of the conditioned and non-conditioned space. Recommendations are also provided on the appropriate technical bulletin for sealing the openings created by the dry sprinkler; if the freezer contains food products, make sure the sealant you use is FDA approved.
Reliable has been a leader for years in solder link technology and solder links are used where appropriate. Solder link sprinklers are somewhat more robust and do not require plastic covers for protection during shipping and installation, saving our customers time and money. Glass bulb sprinklers are available where the needs for aesthetics or other design considerations dictate their use.
Reliable chose many years ago not to compete with our customers, and we do not compete with our customers today. Our mission is to provide customers the latest in quality fire sprinklers, valves, and related products manufactured by Reliable utilizing the latest technology. In addition, Reliable distributes other quality fire protection products manufactured by selected vendors.
Yes. An excellent choice for MRI rooms is the Reliable Model F4FR-NF, a non-ferrous concealed sprinkler specifically tested for use in MRI rooms. This concealed sprinkler has been tested in a laboratory with a magnetic field of 6 Tesla. The clinical magnet systems commercially available today produces a magnetic field of approximately 3 Tesla.
Beginning in January of 2001, all sprinkler manufacturers were required to assign an alpha-numeric code called the sprinkler identification number (SIN) to each sprinkler. This was to comply with the marking requirements found in NFPA 13. When used with the corresponding technical bulletin, the SIN is used to verify the model, deflector style, K-factor and thermal sensitivity of the sprinklers. Reliable sprinkler identification numbers begin with either “R” or “RA” and are followed by three or four numbers. The SIN is marked on the sprinkler deflector.
The “R” and “RA” were historically used to distinguish between revisions of a sprinkler or to designate the appropriate Technical Bulletin associated with a sprinkler. Historically, the first two numbers in the SIN corresponded with the last two numbers of the associated technical bulletin. As the Reliable product line expanded, the “RA” designation was used to provide an additional set of SIN to correspond with additional technical bulletin numbers. For new sprinkler models, Reliable has returned to the use of the “R” designation with three numbers that no longer correspond with the associated Technical Bulletin.
The sprinkler identification number (SIN) number is used only to verify the model, deflector style, K-Factor and thermal sensitivity of the sprinkler. The SIN does not identify the temperature rating, trim style, decorative finish and/or corrosion-resistant finish of the sprinkler. This level of information would result in a potentially infinite number of very long SINs that could not be reproduced on a relatively small device.
Sprinkler identification numbers are a unique combination of sprinkler attributes that, over time, are subject to change or obsolescence. The current version of SIN 3625 is the Reliable Model F1FR56 upright sprinkler (SIN RA1425) which can now be found on Bulletin 074. Please refer to this document for additional information about our full range of sprinkler identification numbers.
No, installation of the retaining flange is not a UL Listing requirement. The tamper resistant and self-injury prevention features of institutional sprinklers are not part of the UL Listing. They are design features provided by the sprinkler manufacturer. For maximum tamper resistance, it is the responsibility of the installing contractor to secure the nipple on which the sprinkler is installed to prevent the sprinkler and escutcheon assembly from being pulled away from the wall or ceiling. The retaining flange is provided as a way of securing the branch line piping, in the form of a nipple or arm-over, to prevent pipe movement initiated by the room occupant. If the retaining flange cannot be used due to larger piping or over-sized wall sleeves, alternative devices approved by the installing contractor or design engineer may be used to secure the piping from movement.
No, there are no listed/approved sprinkler guards for institutional sprinklers. By design, a sprinkler guard would provide an attachment point for an individual intent on inflicting self-injury. In addition, features for such a sprinkler guard would impede and hinder sprinkler performance.
No, there are no listed/approved sprinkler guards for extended coverage or residential sprinklers. Because of the extended discharge requirements and low flow characteristics associated with these types of sprinklers, the sprinkler guard would act as a significant obstruction to sprinkler performance, requiring greater flows and pressure to meet listing/approval requirements.
No, corrosion-resistant coatings adversely affect the sensitivity of the fast-response fusible link. Currently, corrosion resistant listings can only be obtained for quick-response sprinklers using a glass bulb thermal element.
Sprinkler temperature rating is based on the following:
- Maximum expected ambient temperature a sprinkler will be exposed to on a daily (or seasonal) basis
- Proximity of sprinklers relative to heat sources
- Design densities chosen for storage applications based on storage area/density curves
NFPA 13 (2022) section 7.2.4 provides the information necessary for selecting the proper temperature rating for fire sprinklers regarding ambient temperature and proximity to heat sources. Tables 7.2.4.1 (a) & (b) were added to clarify different temperature requirements when using a glass bulb or solder link thermal element. Chapters 20 through 26 contain information about temperature selection of sprinklers used in storage occupancies.
Testing of residential sprinklers has shown that the listed flows and pressures for flat ceilings provide an acceptable level of protection in most sloped and/or beamed ceilings. The current editions of NFPA 13D, 13R & 13 allow listed residential sprinklers to be installed at their listed flows and pressures for ceiling heights up to a maximum 24′ ceiling height:
· Flat, smooth, horizontal ceilings with no beams
· Flat, horizontal beamed ceiling with beams up to 14” deep and sprinklers below the beams
· Maximum 8:12 smooth, sloped ceiling with no beams
· Maximum 8:12 sloped ceiling with beams up to 14” deep and sprinklers below the beams
· Maximum 8:12 sloped ceiling with beams of any depth with sprinklers in each pocket created by the beams
Additional constraints apply to these brief descriptions, and it is the contractor’s responsibility to confirm all requirements from the appropriate NFPA standard with the Authority Having Jurisdiction.
Yes; however, sprinklers are tested and listed/approved by the foam manufacturers with each specific foam concentrate. You must reference the UL Fire Protection Equipment Directory section on Foam Liquid Concentrates (GFGV), the Factory Mutual Approval Guide, and/or the foam manufacturer’s technical documentation to determine which sprinkler is listed/approved for use with each specific foam concentrate.
Yes, section 9.4.3.5 of NFPA 13 (2022 edition) clarifies that it is acceptable to install sprinklers that carry listings for quick response and standard response for different coverage areas in the same compartment without any separation required.
No, Factory Mutual does not currently recognize any fully concealed sprinklers as quick response. The Reliable G5-56 carries both an FM (SR) approval AND a UL (QR) listing. The G5-56 meets both FM & NFPA-13 requirements. Keep in mind two separate calculations may be required to satisfy both entities. If a different K-factor is needed, verify that K-factor meets both UL & FM requirements. If not, a discussion with the local AHJ & FM Global is required to decide between satisfying the NFPA Standards or FM Global. In most cases, the national NFPA standard will take precedence.
No. Concealed sprinklers are tested during the listing/approval process with a ceiling installed and rely on the surrounding ceiling to assist in the movement of heat past the thermal element. There is no testing protocol for concealed sprinklers to be installed without a ceiling.
Yes and No. Reliable can provide guards for the Models P22 & P25 ESFR sprinklers when they are used as in-rack sprinklers. Guards cannot be installed on ESFR sprinklers when they are used for ceiling protection due the negative impact of the sprinkler spray pattern created by the guard.
This issue is addressed in NFPA-13 (2023), 30.3.6 and NFPA-25 (2023), 5.4.1.3.2: Where replacing residential sprinklers manufactured prior to 2003 that are no longer available from the manufacturer and that are installed using a design density less than 0.05 gpm/ft2 (2.o4 mm/min), a residential sprinkler with an equivalent K-factor (± 5 percent) shall be permitted to be used provided the currently listed coverage area for the replacement sprinkler is not exceeded. If a K-factor can’t be found within these parameters, a hydraulic analysis may be needed. That may be as simple as comparing the hydraulic requirements of the existing sprinkler to current sprinkler options. Where questions still arise, consult the local AHJ.
Most sprinklers can be identified using good quality photographs of the sprinkler and sprinkler deflector which can be emailed directly to technicalservices@reliablesprinkler.com. Once identified, a copy of the appropriate technical bulletin will be provided. If not evident on the photographs, the year of sprinkler manufacture should be provided to insure the bulletin edition nearest the manufacturing date is selected.
Reliable offers a wide range of standard finishes as well as custom painting for flat and conical concealed cover plates. In addition, for flat cover plates a standard set of wood grain finishes is available. We also offer custom printed flat cover plates that are computer matched to a material sample provided by the customer. Please reference Bulletin 203 for further finish details.
Information regarding storage, handling, and installation of sprinklers is found on the appropriate sprinkler Technical Bulletin and Caution Sheet 310.
701A is an Underwriters Laboratories (UL) Control Number that was assigned to Reliable many years ago. Although UL has since changed their policies and procedures for new manufacturers, established manufacturers such as Reliable still display the Control Number on many products. 701A is a manufacturers designation and does not provide any product specific information.
Yes, sprinklers are considered new provided they have been properly stored and have not been previously installed. The NFPA-25 timeline on sprinkler life starts when a sprinkler is installed.
Valves
The only difference between these two trims is the addition of a Model E1 Retard Chamber designed to prevent false water flow alarms. In a short term water flow event such as a pressure surge, the retard chamber must fill before the hydraulic pressure can be converted to an alarm signal. If the flow event ends before the chamber fills, no alarm is sounded and the chamber automatically drains.
The DDX-LP Dry Valve provides a number of significant advantages over conventional valves:
- The DDX-LP valve is a latching clapper valve that is less susceptible to false trips.
- The DDX-LP valve utilizes low pneumatic pressure; this results in smaller air compressors or lower nitrogen volume in the system.
- Low pressure systems improve water delivery times; this can result in larger and/or fewer dry systems.
- Low pressure systems can eliminate the need for an accelerator, and when necessary, they are much more easily added.
- Low pressure systems, all else being equal, hold pressure better than conventional systems.
No, the DDX utilizes an intermediate chamber in its seat design, which separates the inside of the valve body with the alarm outlet piping which is open to atmosphere. Supervisory air pressure can therefore fill the valve body and the system piping without separation by a riser check valve.
NFPA 13 requires that all sprinkler systems have provisions to be properly drained. The main drain outlet or drain manifold outlet should be piped outside or to an open drain capable of providing proper drainage for a main drain test. To estimate the total flow from the drain connection of various drain sizes, the following formula can be used:
Q = K√P where
Q = drain flow in gallons
K = Drain angle valve K-Factor (K-Factor based upon angle valve manufacturer’s data)
P = Water Supply Pressure
The air pressure gauge reads the air pressure on the system side of the air supply line check valve only. It does not read air pressure in the line between the air supply and the DDX-LP trim connection. If the DDX-LP valve trips shortly after the water supply control valve is opened, the line between the air supply and the DDX-LP system connection has lost pressure opening the DDX-LP valve pneumatic actuator. The open pneumatic actuator releases the hydraulic pressure in the push rod chamber tripping the valve. To properly diagnose air supply issues, a pressure gauge should be installed on the airline between the compressor and the check valve on the back side of the DDX valve.
Valve Accessories
The pressure switch used on the Model B pressure maintenance device is a Furnas Model 69H, preset to maintain a nominal system pressure of 35 PSI. If it is necessary to adjust the pressure setting, remove the cover and locate two adjustment screws. The large metallic screw is for adjusting the cut-in and cut-out pressures together. Cut-in pressure is defined as the pressure at which the compressor comes on as system pressure decreases; cut-out pressure is defined as the pressure at which the compressor shuts off as system pressure increases. Turn the large screw clockwise to increase both cut-in and cut-out pressure; counterclockwise to decrease both the cut-in and cut-out pressures. The small metallic screw is for adjusting the differential pressure. Differential pressure is defined as the difference between the cut-in and cut-out pressures. Turn the small screw clockwise to increase the cut-out pressure without affecting the cut-in pressure; counterclockwise to decrease the cut-out pressure without affecting the cut-in pressure. It is important that a minimum differential pressure of 7 psi or more is maintained between the cut-in and cut-out pressure settings to avoid “chattering” of the pressure switch contacts. Below 7 psi, chattering of the pressure switch contacts may occur as the pressure approaches the cut-out pressure. This will cause the compressor to cycle on and off rapidly which may damage the compressor motor.
There is no difference in the accelerator model used with these systems. Each system uses the Reliable Model B1 Accelerator when a quick opening device is needed. The trim associated with the accelerator for each system is different, however, as well as where the air pressure is directed from the outlet of the accelerator. When used with a Model FX dry valve, air pressure flowing through the accelerator is directed into the intermediate chamber of the dry valve. Pressurizing this chamber destroys the differential between the air side and the water side of the clapper causing the dry valve to trip faster. On the DDX systems, the accelerator is located on the air supply line feeding the actuator, and the outlet piping is open to atmosphere. The DDX systems utilize a hydraulically operated valve, and the actuator is the releasing device for the system. The faster the air pressure is removed off the air side of the actuator, the faster the DDX valve trips. When the accelerator operates, it exhausts the air pressure off the air side of the actuator to atmosphere causing the valve to trip faster. Subsequently, there is less trim associated with the accelerator for the DDX systems than for the Model FX dry valve.
Beginning with the 2025 Edition of NFPA 13, air compressors dedicated to sprinkler systems are required to be listed. Compressors were not previously required to be listed and/or approved. Air compressors must have enough capacity to restore operating air pressure in dry pipe and double interlock preaction systems within the time limits specified in NFPA 13. When the capacity of the air compressor is 5.5 CFM @ 10 PSI or higher, NFPA 13 requires the use of an air receiver and a listed pressure maintenance device with the compressor. The Reliable Model A pressure maintenance device is listed to regulate system pressure between 5 and 75 PSI (0.34 to 6.9 bar) with a maximum inlet pressure of 175 PSI (12 bar).
There are four common arrangements used for maintaining system air pressure: (1) The Reliable Model A Pressure Maintenance Device (PMD) can be used to regulate pressure from a dependable plant air system that incorporates a tank, (2) The Reliable Model A PMD can be used to regulate pressure from a dedicated tank-mounted air compressor that incorporates a pressure switch capable of automatically maintaining tank pressure, (3) The Reliable Model B Air Maintenance Device incorporates a pressure switch that can start and stop a “bare” compressor, and (4) a standalone compressor that incorporates a pressure switch to start and stop the compressor. It is important to note that when the compressor capacity is 5.5 CFM @ 10 PSI or greater, an air receiver tank and a listed air maintenance device for each system is required by NFPA 13. It is also important to note that when a tank is not used on the system, the pressure will not be constant and will vary within the on/off settings of the pressure switch. A tank mounted compressor with a Reliable Model A PMD provides constant system pressure and is a “best practice” combination that works in all cases.
Most systems can utilize any compressed air system meeting the requirements of NFPA 13 that are capable of maintaining the required system pressure. Some systems such as the Reliable Type D Double Interlock system, however, require a tank mounted compressor since this system is only listed for use with the Reliable Model A PMD provided with the trim.
The condition you describe is called “short cycling.” Short cycling typically occurs when the pressure control switch is sensing pressure in a very small volume of space that is not holding full pressure. The compressor turns on upon loss of pressure, and the small volume of space is pressurized within a few seconds. This satisfies the pressure switch which then turns the compressor off. When the small volume of space loses pressure, the cycle repeats. By isolating each independent section of air line (between control valves, check valves, regulators, etc.), you generally can locate which fitting or device is failing to hold pressure.
This condition can also be caused by using the Reliable Model A Pressure Maintenance Device with a tank-less air compressor. The mechanical regulator severely restricts air flow and allows the upstream piping to pressurize very quickly at which time the compressor turns off. The regulator then bleeds air into the system lowering the pressure on the upstream side and the compressor turns on. Depending on the demand on the downstream (system) side of the regulator, this cycle could continue indefinitely. The Reliable Model A PMD is not designed for use with tank-less compressors.
The flow switches used on these devices becomes part of a listed “assembly” that has been tested and accepted by a recognized agency. When used independently of the listed assembly, the flow switch must be installed in accordance with the particular listing requirements provided by the manufacturer of the switch.
A number of factors are involved with how quickly water can be delivered to the inspector’s test from the dry valve, but the first step is to review the requirements of NFPA 13:
- Systems of 500 gallons or less can be installed without an accelerator and are not required to meet a specific water delivery time.
- Systems over 500 gallons but not over 750 gallons are not required to meet a specific water delivery time when equipped with a quick-opening device (accelerator).
- Systems over 750 gallons are required to meet the water delivery times specified in NFPA 13 (2013) section 7.2.3.
The generally accepted practice for systems over 500 gallons is to install the system without an accelerator and perform the trip (or water delivery) test. If water delivery time exceeds the specified limits, install an accelerator. For 500 to 750 gallon systems, this is all that is required. For systems over 750 gallons, rerun the water delivery test after installation of the accelerator to verify the improved performance.
It is important to note that the Reliable Model B1 accelerator requires the use of a tank-mounted compressor and Model A Pressure Maintenance Device. The accelerator reacts on a “shock” of pneumatic pressure, and a system that is either on or off (even within the settings of the pressure switch) will cause the accelerator to false trip. For this reason, it is advisable to use a tank-mounted compressor and Model A Pressure Maintenance Device for all systems over 500 gallons capacity.
The hole goes to the top and will be visible prior to reassembling the diaphragm and top chamber cover.
The minimum air or nitrogen pneumatic pressure must be 15 psi (1.0 bar) to ensure proper accelerator operation. The maximum air or nitrogen pneumatic pressure should not exceed 75 PSI. Please refer to bulletin 323 for additional information.
For systems that utilize an LP dry pilot actuator as a tripping mechanism, a minimum of 8 PSI and a maximum of 30 PSI of supervisory air or nitrogen pressure is required. The pressure must never be less than that specified in the Technical Bulletin relative to the incoming water pressure. Over-pressurization of the Model LP actuator can result in damage to the diaphragm. A tank mounted air compressor and an air maintenance device that maintain a constant pressure are recommended.
Provided the generator is not capable of producing more than 5.5 CFM at 10 PSI, a reserve tank is not required, however, best practice dictates that a reserve tank with a mechanical regulating device will result in more stable and reliable operation of the system. Reserve tanks also provide a limited standby source of pressure during short term power outages. For that reason, Reliable highly recommends a reserve tank on ALL pneumatically pressurized systems.
The Model C Ball Drip is designed for use primarily on fire department connection lines to drain the section of pipe between the FDC and the check valve. It locks closed under pressure but automatically relieves residual pressure after the FDC use. The Model D Mechanical Ball Check Valve is used on water control valve alarm lines to capture and hold pressure on alarm devices until being manually opened by pushing the plunger on the valve.
The Model A Pressure Maintenance Device is designed for use where a constant source of compressed air or nitrogen is available, such as automatic tank-mounted compressors or nitrogen tanks. The Model A will maintain a constant pressure in the system regardless of pressure fluctuations in the compressed air or nitrogen source. The adjustable pressure range for the Model A is 5 to 100 psi (0.34 to 6.9 bar).
The Model B Air Maintenance Device is used when a small tank-less air compressor without a start/stop pressure switch is used. By wiring the compressor motor to the electrical pressure switch of the Reliable Model B Pressure Maintenance Device, the compressor is controlled by the pressure in the dry pipe system or dry pilot line. The adjustable pressure range for the Model B is 14 to 60 psi (1.0 to 4.1 bar).
Special Hazards / Special Systems
Double Interlock describes a type of preaction system that requires two events to coexist before the deluge valve will open and allow water to flow into the sprinkler piping. A good analogy is a door with two locks—both must be unlocked before the door will open. Double Interlock preaction systems were originally developed for freezers and refrigerated warehouses but are often specified for computer rooms. Some approval authorities, however, continue to limit their use to freezers and refrigerated warehouses.
The Potter PFC 4410 is a listed “release control” meeting the requirements of NFPA standards for preaction and deluge system control. The latest version (PFC4410G3) comes standard with six preprogrammed water release programs that meet a wide range of applications, and also has custom programming capability. The panel is compatible with a variety of detectors and more importantly, it is compatible with the standard solenoid valve used in most Reliable special systems.
NFPA 13 states that a compressor must have the capacity to restore the required system pressure within 30 minutes, except for refrigerated spaces maintained below -5°F, in which case the time requirement becomes 60 minutes. To properly size the compressor, you must calculate the volume or capacity of the entire sprinkler piping system in cubic feet. Once this is known, calculate the cubic feet per minute necessary by dividing the capacity of the system by the time requirement listed above, and then select a compressor based on the cubic feet per minute of compressed air it provides at the required system pressure. To determine the volume limitations stipulated by NFPA 13 for dry and double interlock preaction systems, the total piping volume must be converted from cubic feet to gallons (1 ft³ = 7.48 gal.).
NFPA 13 states that the compressor must have the capacity to restore the required system pressure within 30 minutes, except for refrigerated spaces maintained below -5°F, in which case the time requirement becomes 60 minutes. To properly size the compressor, first calculate the volume or capacity of the entire sprinkler piping system in gallons and then convert to cubic feet (1 gallon = .1337 ft³). Once this is known, calculate the cubic feet per minute (CFM) necessary from the compressor by dividing the capacity of the system by the number of minutes required (see above). Next, select a compressor based on the cubic feet per minute of compressed air it provides at the required system pressure. To determine the volume limitations stipulated by NFPA 13 for dry and double interlock preaction systems, the “Water Delivery Time” must be in strict accordance with NFPA 13 for the protected hazard.
In addition to providing enhanced protection against corrosion, galvanized trim is a requirement in those jurisdictions following The National Fire Alarm Code NFPA 72 which requires that piping between the sprinkler system and a pressure actuated alarm initiating device shall be galvanized or of nonferrous metal or other approved corrosion-resistant material of not less than 3/8″ nominal pipe size.
Reliable offers two standard solenoid valves depending on the pressure rating required for the system. Both are ½” NPT valves manufactured by Skinner, a division of Parker Hannifin Corp. For systems not exceeding 175 psi operating pressure, Reliable uses a 24VDC normally closed, pilot operated solenoid valve that requires a .41 amp holding current and 10 watts power. The Skinner model number is 73218BN4UNLVN0C111C2. For systems not exceeding 300 psi operating pressure, Reliable uses a 24VDC normally closed, pilot operated solenoid valve that requires a .83 amp holding current and 22 watts power. The Skinner model number is 73212BN4TNLVN0C322C2.
Definition of interlock: To lock together; to connect so that the motion or operation of any part is constrained by another.
Preaction systems are interlocked systems that require a supplemental detection system in the same area as the sprinkler system. Operation of the deluge (preaction) valve is dependent upon activation of a detector, or both a detector and a sprinkler.
Single interlock preaction systems require a single event –a detector to operate –in order for the deluge (preaction) valve to trip. The detection system is designed to be more sensitive than the fire sprinklers and should operate first. Once the valve trips, water fills the system piping. Water will not be discharged until a sprinkler operates due to the increasing heat of the fire. Given that water is present at the sprinkler at the time of sprinkler operation, single interlock preaction systems are treated as wet systems from a design standpoint.
Double interlock preaction systems require that both a detector AND a sprinkler operate before causing the valve to trip. A good analogy is a door with two locks—both must be unlocked before the door will open. Once the valve trips, water will flow into the system piping and immediately discharge out of the open sprinkler(s). Given that the water is held at the valve until the sprinkler operates, double interlock preaction systems are treated as dry-pipe systems from a design standpoint, and all of the rules governing the design of dry-pipe systems must be applied to double interlock preaction systems.
Double interlock preaction systems require two events to occur before the deluge (preaction) valve actuates: operation of the detection system and activation of one or more fire sprinklers. The detection system is more sensitive than the sprinklers and operates first. Subsequent activation of the sprinkler causes the supervisory pneumatic pressure in the system piping to decrease. This decrease in pressure is the second interlock which causes the deluge (preaction) valve to trip. The difference between the Type D and Type F double interlock preaction systems is based on the method of detecting the decrease in pneumatic pressure.
On the Type D system, the decrease in pressure is sensed by a pressure switch installed on the pneumatic supply trim piping. When the pressure switch activates, it provides a second signal to a cross-zoned releasing panel, causing the releasing circuit to energize the solenoid valve and open the deluge (preaction) valve. The Type D system is commonly referred to as electric/electric type system, and is recommended for data room protection.
On the Type F system, the solenoid valve opens immediately upon activation of the detection system, however, a mechanical device (low-pressure pneumatic actuator) is installed downstream of the solenoid valve. This valve is held closed with system pneumatic pressure. The opening of one or more fire sprinklers results in the loss of pneumatic pressure thereby allowing the actuator to open. This in turn causes the push-rod chamber of the deluge (preaction) valve to depressurize and the valve to open. The releasing panel does not have to be configured for cross-zoned operation on the Type F system. The Type F system is commonly referred to as electric/pneumatic type system, and is recommended for freezer protection.
The Reliable Type PL double interlock system is a pneumatic/pneumatic system that does not utilize electric detection. Instead, this system uses a dry pilot line with Fixed Temperature Release Pilot Line Detectors (FTR-PLD). These ultra sensitive devices are similar to a fire sprinkler but are not relied on for water discharge. Installed on ½” or larger piping in the protected area and pneumatically pressurized, they form a mechanical detection system. The pilot line is connected to one chamber of a dual chamber, low pressure actuator, while the second chamber is connected to the system that also contains pneumatic pressure. Only when both zones lose pneumatic pressure can the deluge (preaction) valve open. Activation of one or more FTR-PLDs results in loss of pressure in one zone, and subsequent activation of one or more fire sprinklers on the system due to increasing heat from a fire results in loss of pressure in the second zone. Loss of pressure in both zones allows the actuator to open and depressurize the push rod chamber of the deluge (preaction) valve allowing it to also open.
The Reliable Type PL double interlock system is particularly well suited for locations where the power supply is considered unreliable or where there is risk of explosion due to electrical sparks. Because the detection system is consists of pipe, hangers, and fittings, the fire sprinkler contractor maintains complete control over an otherwise time-consuming, challenging electrical scope of work.
The second releasing event for Type D systems is the activation of the low-pressure switch on the pneumatic supply piping to the system caused when one or more fire sprinklers open. To make sure the low-pressure switch operates in a timely and consistent fashion, a steady and consistent pressure must be maintained on the system. A tank-less air compressor operates within a range of pressures. For instance, the compressor may be set to start at 20 PSI and stop at 30 PSI. If the low-pressure switch were set at 15 PSI, the system would have different reaction times depending on whether the system pressure was 30 PSI or 20 PSI at the time of a fire. For this reason, a pressure maintenance device is provided and required as part of the listed Type D assembly..
No. Deluge and single interlock preaction systems may utilize mechanical detection in the form of wet pilot (hydraulic) or dry pilot (pneumatic) lines. Only electrically operated deluge and preaction systems that utilize solenoid valves on the release trim require a listed release control panel for operation of the system. Pneumatic/pneumatic type double interlock preaction systems such as the Reliable Type PL also use mechanical detection and do not require a release panel.
NFPA requires the releasing control panel to be listed/approved with the releasing device (solenoid valve) in electrically operated systems. Control panel manufacturers often have a list of compatible releasing devices (solenoid valves) that are listed/approved with their panels. Refer to Reliable Bulletin 718 for solenoid valve options offered by Reliable. Note that it is the control panel manufacturers that get solenoid valves listed with their panels, and not fire protection valve manufacturers that get control panels listed with their valves.
The Model DDX deluge valve is a hydraulic piston operated, mechanical type deluge valve. When the side chamber of the Reliable Model DDX Deluge Valve is pressurized, hydraulic supply pressure acts on the piston and pushrod assembly to hold the clapper closed. The Model DDV deluge valve is a diaphragm-type deluge valve. The valve diaphragm seals against a seat machined in the valve body. Water pressure in the chamber between the diaphragm and the cover presses the diaphragm against the seat to prevent water flow through the valve. Diaphragm deluge valves offer the ability to control the valve (on/off) from a remote location.